The story of the Gentle stretcher
24 April 2025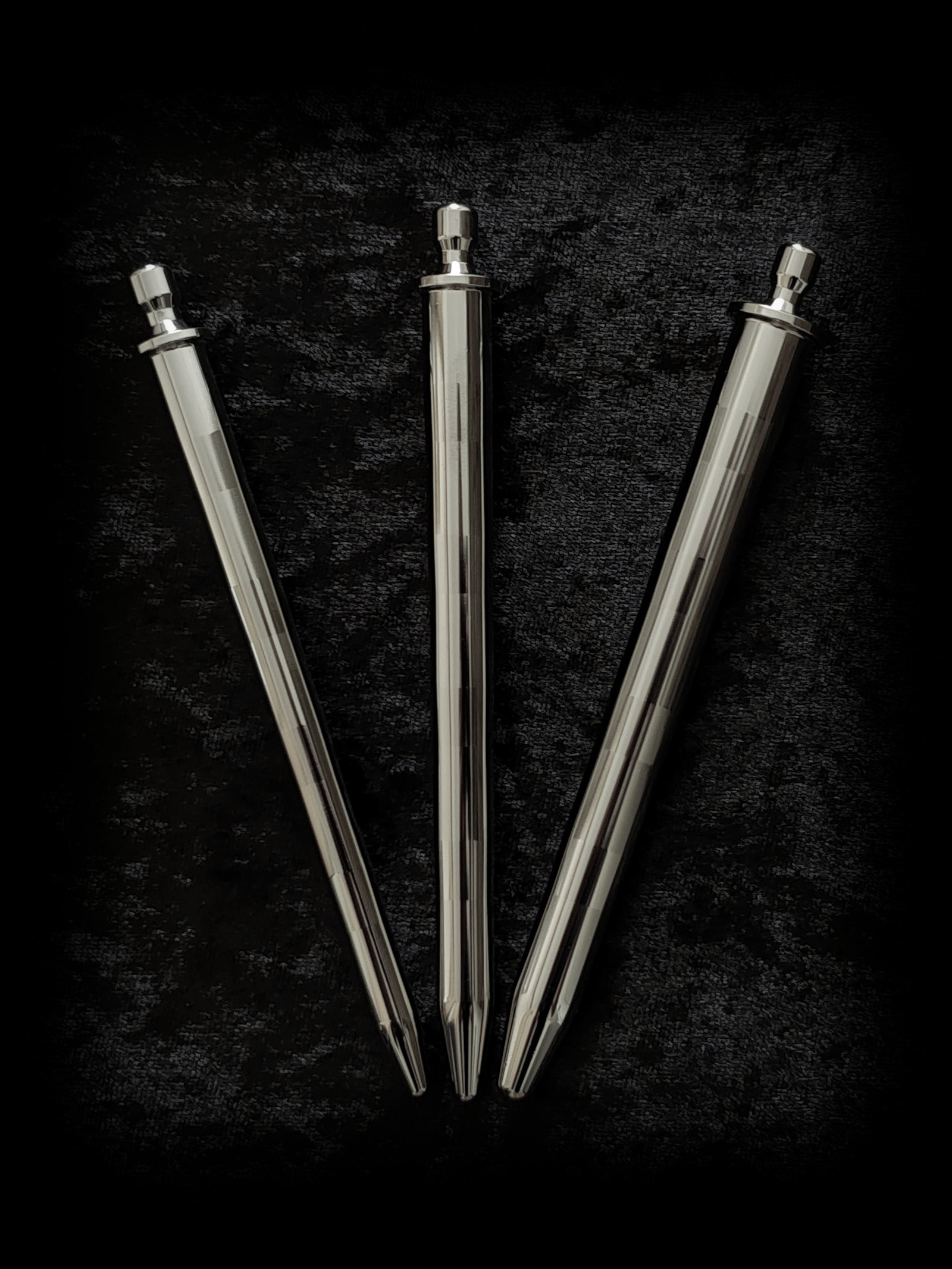
The next option was variable-width toys, featuring various screw-action mechanisms that induced tension. However, they were difficult, if not impossible, to fix in place, scratched a lot, and some even became infamous for pinching the urethra.
Last but not least, there were stepper sounds. But these only came in large increments of 1 mm or more! Anyone who's tried using a double-sided Hegar sound knows that going past the middle might not be as enjoyable as expected. And now, let me stop here and talk about Hegars for a moment. What are you supposed to do when you want to move to the next size?
Well... unfortunately, the answer is: nothing. They simply weren't designed to be used that way. And so, the journey of the Gentle Stretcher began.
The basic specification was simple — create a sound which has:
- An increasing diameter
— but not in short or large steps. - A linear taper tip
— for better control during insertion. - Alternating straight and tapered stages
— to allow for relaxation and to mark progress.
There are many companies with a lot of machining equipment out there, but not everyone is willing to do individual batches or custom products. After emailing dozens of companies, I finally managed to get the first prototype. It was far from perfect and, quite surprisingly expensive — but it was the beginning...
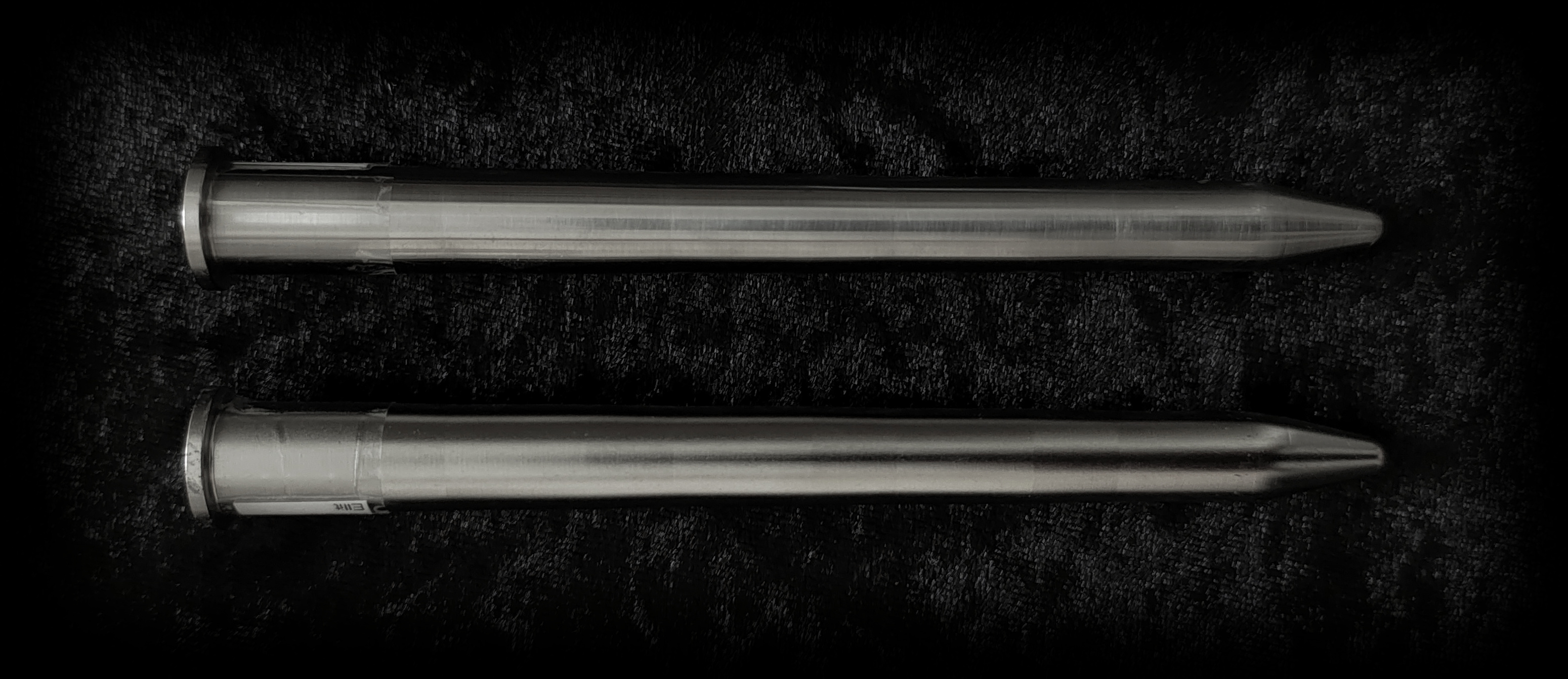
The first prototype
Machined out of stainless steel on a CNC lathe, it had the right shape, but the surface was very rough. Two specimens were made: one polished and one raw. Unfortunately, the polishing process was so crude that it left the surface scratched and far from smooth.Another issue was the marks imprinted by the machine, as it needed to be readjusted during manufacturing.
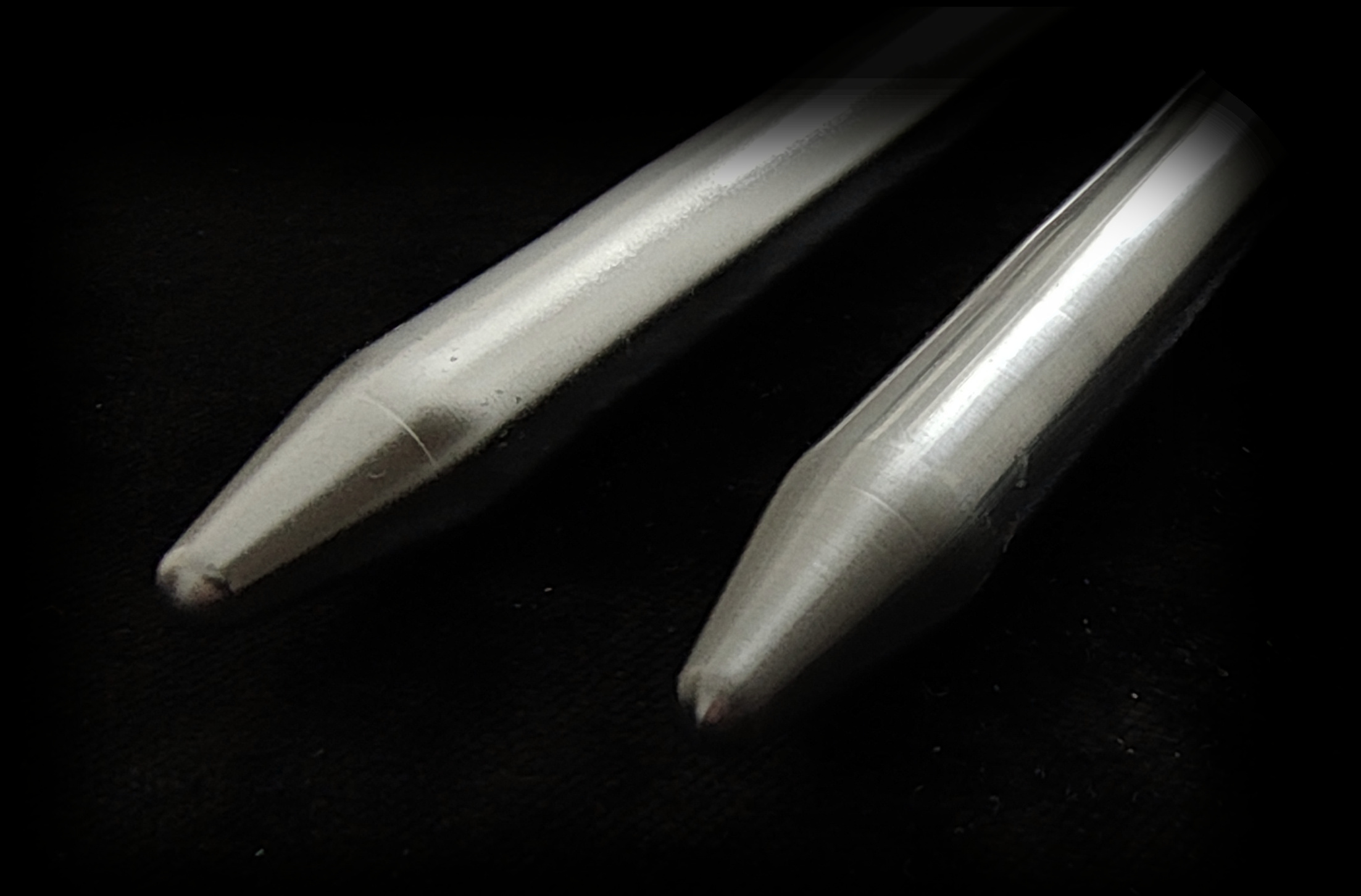
Adjusting the shape
As crude as it was, I started consulting with various specialists on what could be improved, and the project gained considerable momentum. What started as a hobby was growing and eventually became a company. We remodeled the tip, as it seemed a bit too harsh, making it longer and the transition smoother.We also introduced the handle found on the final Gentle stretcher and found a better way of manufacturing the sounds — without readjusting during turning. This required involvement of specialized machines, which unfortunately don't run in small numbers. So we had to scale up.
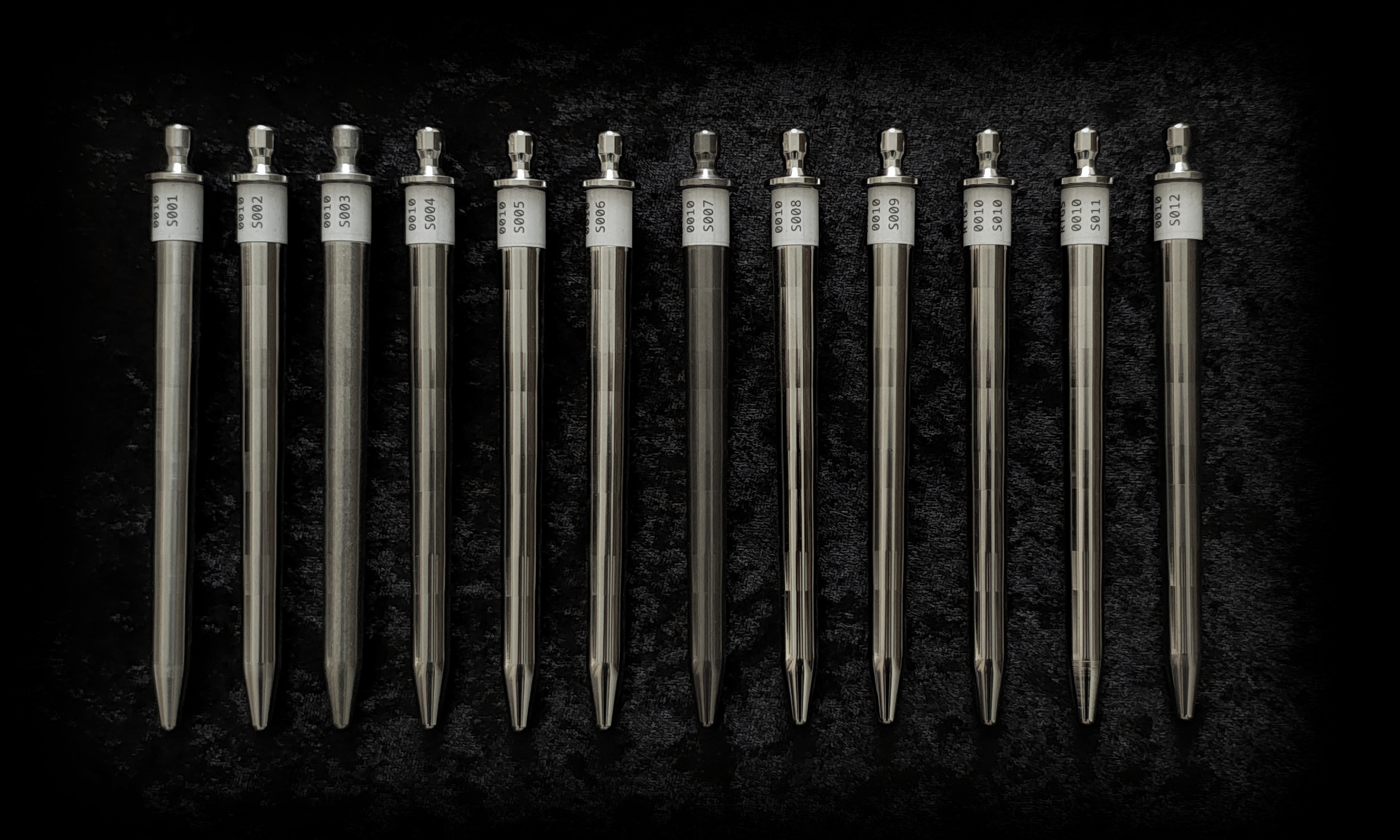
Finding the right surface treatment
We had the right shape, but the surface was still far from ideal. After finding the right machinist, it was time to find yet another specialist who could make it shine. We tested many different processes, and eventually, a collaboration began with a new partner — an expert in medical tool manufacturing.Together, we developed a four-stage grinding and polishing process that leaves the surface incredibly smooth. This special treatment not only enhances comfort but also improves safety by making cleaning easier and increasing corrosion resistance.
A glance into the future
The Gentle stretcher is ready to be sold, but its journey is still in the beginning. We’re constantly working to improve our product and come up with new innovations. Plans are already in motion to introduce more sizes, different shape options, and surface treatments. We look forward to sharing more in our next blog article, so you can be part of the journey as well.Happy sounding,
Chris from ROKITO